Main Technical Achievements M42
Multifunctional carbon fiber reinforced polymers (CFRPs) with enhanced performance (INEGI)
Through the combination of pristine carbon fibres (CFs) with nanomodified resins and sized CFs with unmodified resin, INEGI developed different types of multifunctional and multiscale CFRPs with improved mechanical and electrical performance. In the last period, INEGI received and tested different types of modified CFs that were provided by other SmartFan partners: CANOE supplied sized CFs with different percentages of carbon nanotubes (CNTs) and carbon nanofibres (CNFs), while NTUA prepared electropolymerized CFs. After optimization of the processing conditions, prepreg materials and CFRPs were produced for different mechanical characterization, namely tensile at 0° and interlaminar shear strength (ILSS).
According to the tensile results obtained, the sized CFs did not influence the tensile modulus of the material, while the tensile strength increased 8.5 and 12.8 % for CFs sized with CNTs and CNFs. Regarding the ILSS experiments, the CFRPs produced with CFs from CANOE containing only the sizing solution, without nanoparticles, resulted in an ILSS decrease around 7 %, while the introduction of carbon-based nanoparticle restored and/or increased the interlaminar shear strength of the materials. SEM images of the specimens after ILSS testing can be observed in Figure 1, denoting the affinity between the matrix and the CFs. More interesting results were obtained for the CFRP produced with electropolymerized CF from NTUA, with enhancements around 9 %.
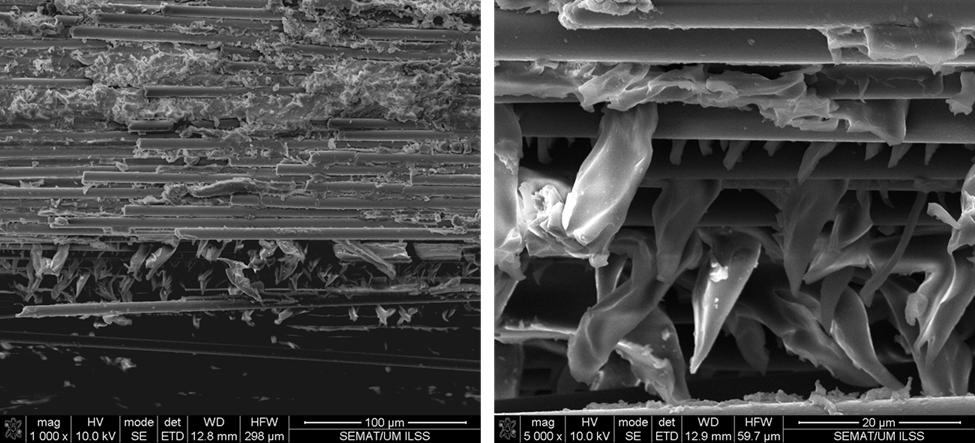
Figure 1
Based on the results achieved throughout the project duration, pre-impregnated materials have been under production in the past months for the preparation of 2 demonstrators (to be manufactured by Dallara): a racing front wing and an energy absorber for the automotive industry.
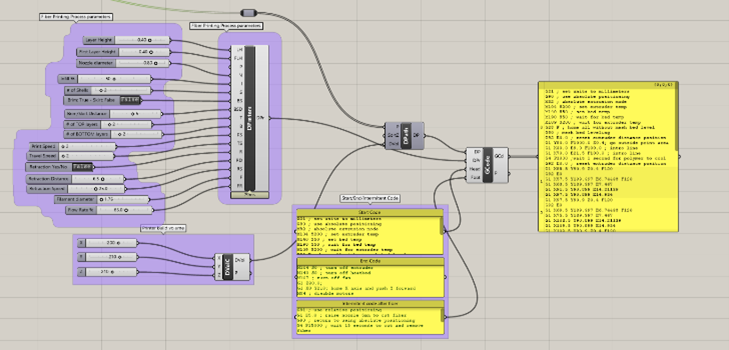
Figure 2: Custom toolpath generation parametric definition
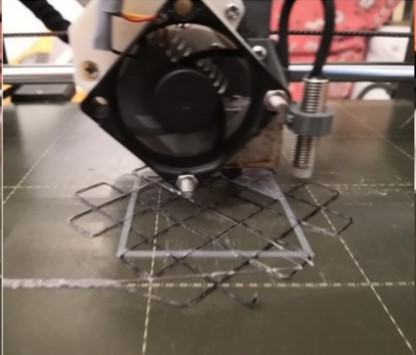
Figure 3: Continuous fiber fabrication using BioG3D’s in-house system
Design of custom toolpath trajectories for continuous fiber 3D printing (BioG3D)
- Within the framework of developing an in-house prototype 3d printer for continuous fiber fabrication BioG3D has worked towards developing a parametric toolset for customized toolpath generation in order to accommodate the particularities of the implemented technology.
- The algorithmic definition receives user input in the form of direct geometries for tool trajectory that the software combines with traditional planar slicing where necessary.
- This specific approach which summarizes the work performed during the past 6 months contributes in achieving the fabrication of free-form, CF composites with continuous fiber reinforcement, by omitting the need for high-priced facilities and equipment, such as autoclaves and complex rigid molds, while combining affordable equipment and advanced feedstock materials for an application-driven production of high-performance components.
- In parallel, experimental validation of the controlled bending response under cooling-heating cycles is in process, for the pre-programmed architectures based on auxetic patterns and continuous fiber embedded patterns with autonomous self-morphing properties.
- The next steps involve the hardware upgrade of the in-house 3d printing system by implementing further design iterations and improved functions, as well as the software optimization and expansion of its capabilities.
Recycling of Thermoset composites (NTUA)
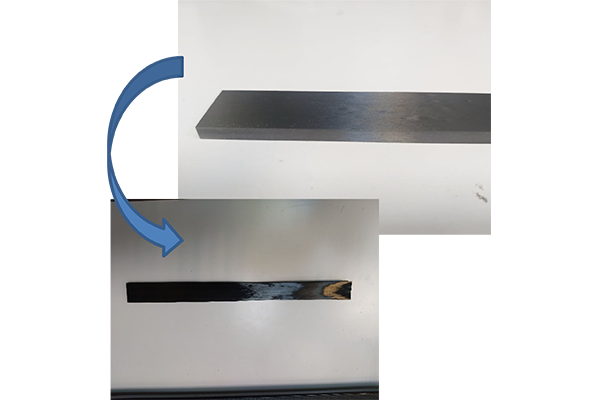
Figure 4: Reclamation from UD composite
Most CFRPs used in high performance applications, consist of a thermoset polymer as matrix, such as epoxy resin. Thermosets have the ability to form cross-links, that offer the needed stability and performance. However, due to their cross-linking nature, their recycling and therefore, the reclamation of their reinforcement states a big challenge, as these matrices cannot be reshaped and remoulded, as thermoplastics do.
NTUA in collaboration with INEGI and DALLARA has achieved, through pyrolysis process, the reclamation of carbon fibre reinforcements from two different CFRPs. One with UD fibres and one with woven fabric reinforcement.
However, pyrolysis process leaves residue from the thermal decomposition of the matrix, such as oils, wax and amorphous carbon. Another challenge that must be addressed, and primitive goal in the thermoset CFRPs recycling, is the maintenance of the mechanical properties of the recycled fibres.
Therefore, further investigation must be performed in order to acquire reinforcement clean from residue and to able to maintain their properties.
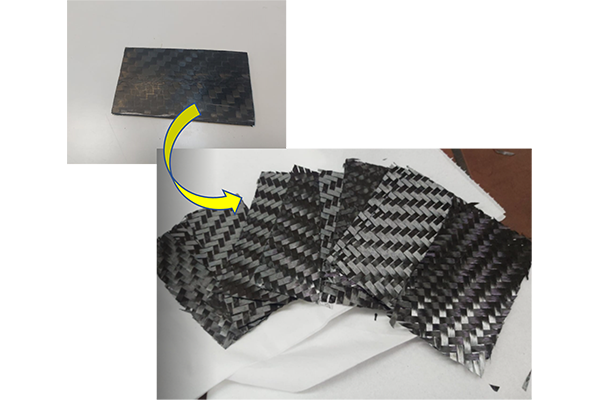
Figure 5: Reclamation from woven fabric composite
Smartfan demonstrator – Front wing for racing cars (DALLARA)
An innovative concept for manufacturing the external shell of a racing front wing with the presence of an undercut was developed. In the last months, the design of the tooling was optimized, ad a cinematic study of the movable parts of the mold was carried out. Tooling were produced in April 2021, and a first prototype of shell with undercut was manufactured with standard Prepreg fabric. Encouraging results were obtained with this first trial. Namely, target geometrical tolerances were achieved as well as an optimal surface finishing.
Further tests will be made in the next weeks, aimed at optimizing the process parameters, such as mold temperature, closure force and curing time. The tooling will be tuned as well in order to minimize the gaps between the parts that are in relative movement.
In the next months, prototypes of this part will be manufactured with unidirectional carbon fibres layers developed in the frame of the Smartfan project.
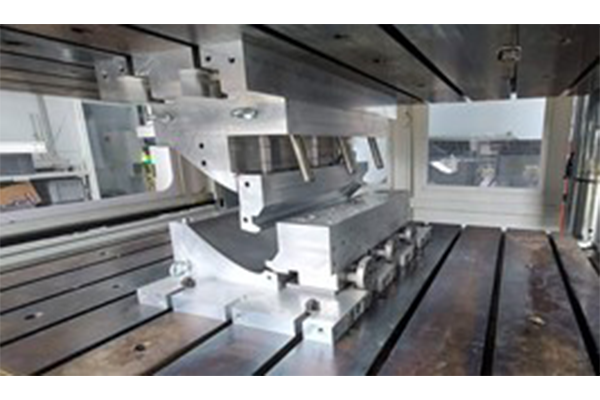
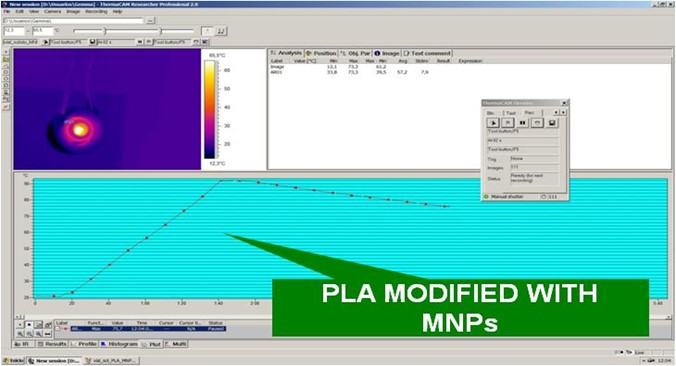
Figure 6: Induction heating trials using thermography
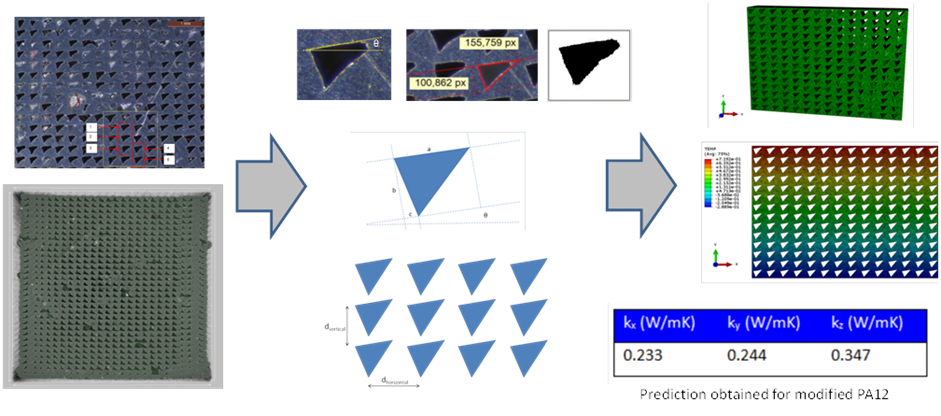
Figure 7: Work-flow followed – example of prediction of thermal conductivities.
New functionalities in polymers and composites, recycling and modelling (ITAINNOVA)
During these last months of the project ITAINNOVA has been working in several tasks:
- Manufacturing of filaments of PLA modified with magnetic nano-particles (MNPs) in order to introduce induction heating capabilities in 3D printing parts. The work done by ITAINNOVA in the project allowed to determine the proper concentrations to achieve adequate heating capacity and printability.
- Study of recycling of nano-modified PLA for 3D printing filaments. Analysis of properties variation considering various recycling steps.
- Prediction of properties of 3D printed nano-enhanced polymers based on modelling. The work done has allowed determining how the internal structure produced by the 3D printing process produces non-isotropic mechanical and thermal properties affected by the printing path. The simulations have been fed with information obtained from the models at lower scales (multi-scale approach considered in SmartFan) and experimental characterizations carried out within the project. This last study will be extended in the next period covering different defects patterns typically obtained in this type of processes.
Spectroscopic assessment of interface quality of modified composites at an early stage/minimizing the need for full scale composite fabrication (FORTH)
In the frame of the SMARTFAN project, FORTH adopts the laser Raman technique to evaluate the interfacial performance of modified composites, well before the actual fabrication of the material. Thus, minimizing the need for full scale testing in every single modified system, saving time and human efforts.
Several different combinations of composite systems provided by other SMARTFAN partners were analysed, including either modified polymeric matrices or modified carbon fibre inclusions.
Regardless the tested material, the mechanism of the method remains the same. A single-filament model coupon is was fabricated and via the Raman acquired shift vs. strain calibration line of the fibre, the calculation of the interfacial strength was possible. The load transfer mechanism in a fibre/matrix system is activated in the vicinity of discontinuities such as fibre ends and/or fibre breaks. The interfacial quality of the model composite directly reflects the mechanical performance of the full-scale composite, providing a great tool towards designing a material according to the desired needs.
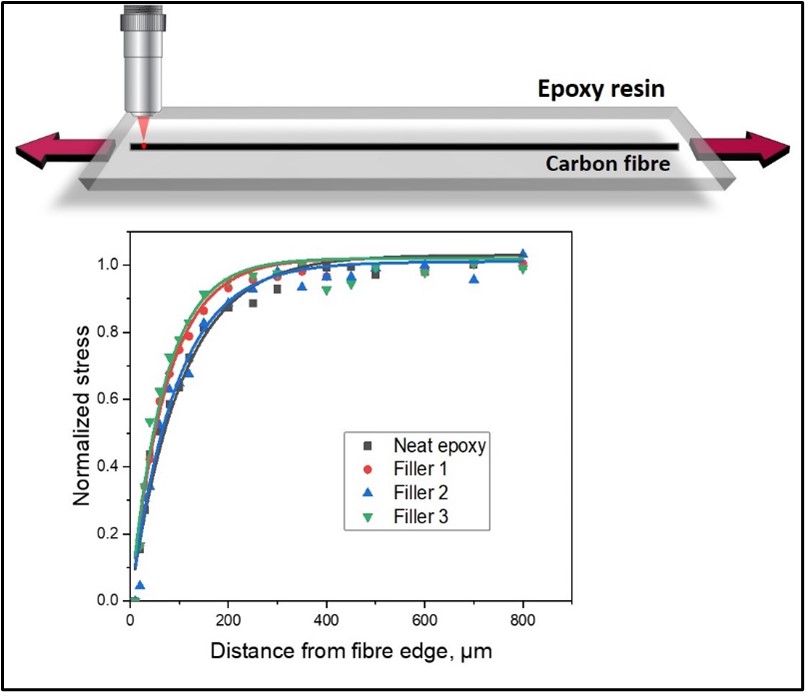
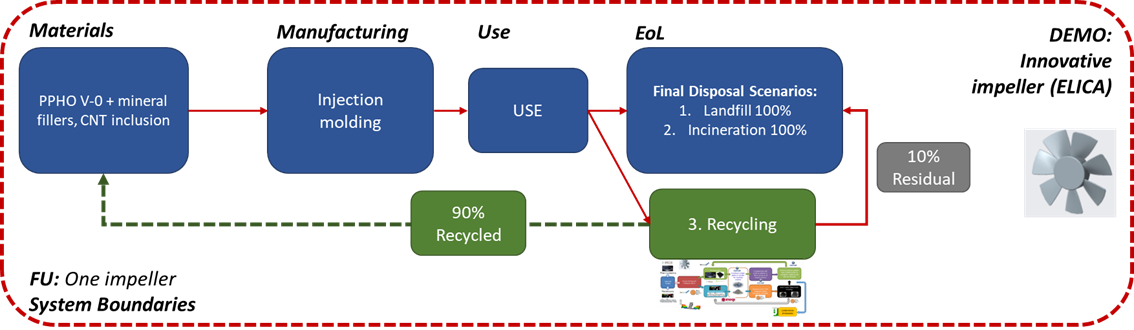
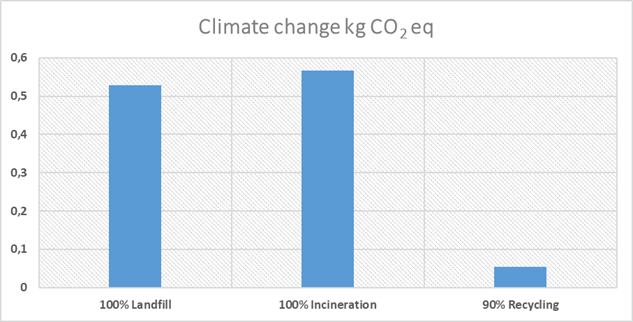
LCA on ELICA’s DEMO concerning the development of an innovative conveyor/impeller for air treatment applications (ELICA)
A cradle-to-grave LCA was performed regarding ELICA’s demo case that focuses on the development of an innovative conveyor/impeller for air treatment applications, based on computational fluid dynamics simulations able to characterize the geometry of the new device taking into account smart materials physical properties and external stimuli as an influence parameter.
- Materials contribute mostly to the environmental impact due to CNT inclusions.
- Municipal waste treatment facilities are considered as the reference EoL scenario for this demo, as it is the dominant waste management pathway to date.
- Recycling seems to be the EoL option with the lowest environmental impact.
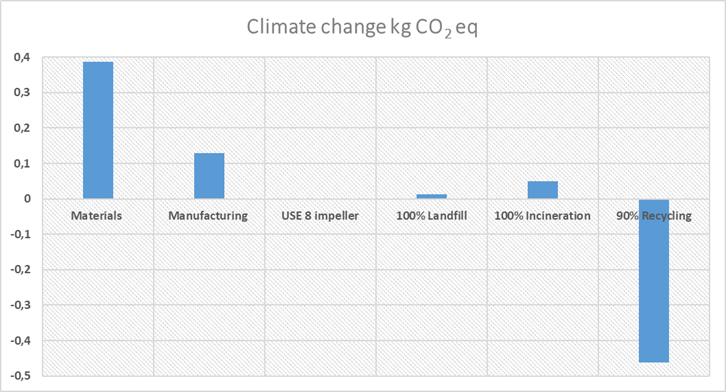
Shape memory polymer composites for large grabbing devices (TOR VERGATA UNIVERSITY)
The Department of Industrial Engineering of the University of Rome Tor Vergata has produced its biggest prototype of smart grabbing device with shape memory polymer composites (SMPC) activated through external heating system. The prototype has a modular structure made of carbon fiber reinforced (CFR) “hands” and a pentagonal base, and shape memory polymer composite (SMPC) hinges. Compression molding was used to manufacture carbon fiber laminates with and without interposed shape memory layer. The proposed architecture allows to obtain a reliable structure able to grab and maintain medium size objects also with complex shapes. External power supply device was used to provide the required voltage (23 V) to the external heating system in the form of flexible heaters fixed on the external surface of the SMPC hinges to allow their memory and recovery steps. Different tests were performed to evaluate both the recovery and the grabbing abilities of the device.
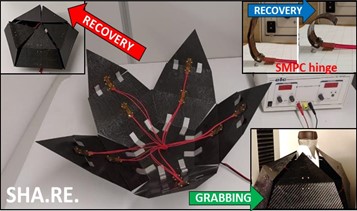