Main Technical Achievements M30
Comparative cradle-to-gate LCA approach of PA, PLA and PP reinforced with CFs, CNTs & GNPs filaments (IRES)
- Climate change, fresh water & Marine eutrophication, Freshwater ecotoxicity, Land use and Mineral fossil & ren. Resource depletion impact categories were selected as the most affected among others.
- CF, CNTs & GNPs production has a clear environmental hotspot over the composite filament production processes.
- Reinforced PA has the highest environmental impact on climate change independently of the type of reinforcement due to the fossil fuel origin production and the related emissions to air, water and soil.
- PA, PLA and PP with GNPs present higher environmental impact compared to the other reinforcements in fresh water eutrophication, marine eutrophication and land use.
- PA, PLA and PP with CNTs mainly affect the fresh water ecotoxicity.
- The majority of the developed composite filaments have a high impact on Mineral eutrophication and Fossil & renewable resource depletion.
- Accounting for all impact categories and assuming equal weight, PP with 3% CFs filament seems to be the most preferable option based on the decision making process through the LCA approach.
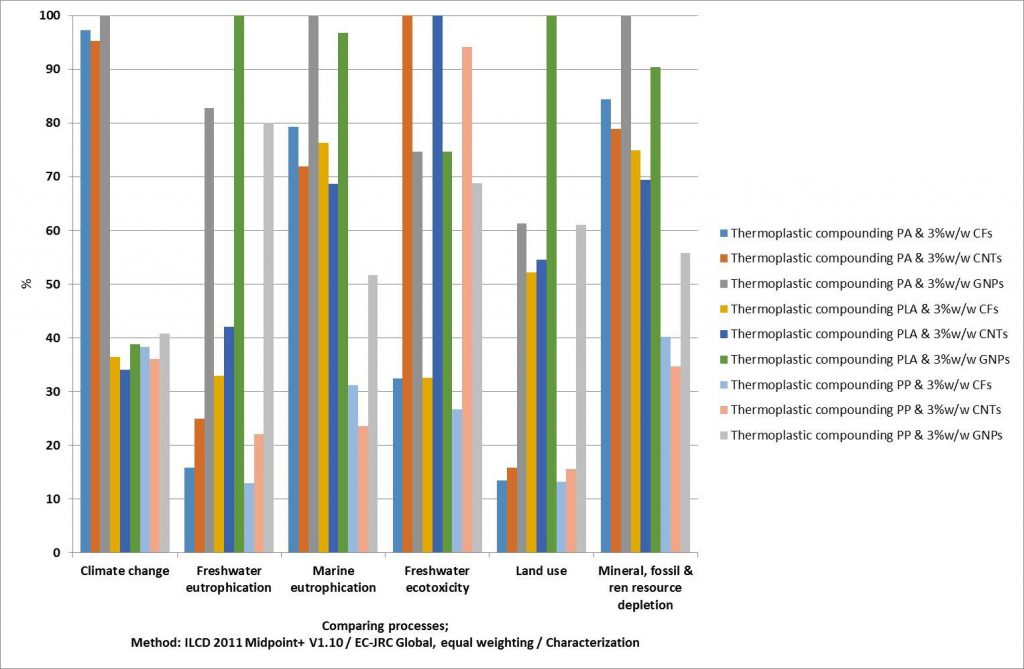
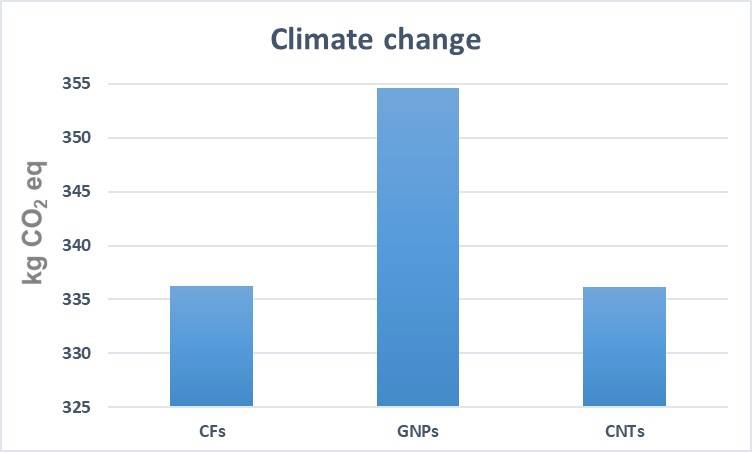
Front wing demonstrator (DALLARA)
An innovative front wing for racing cars has been developed as a demonstrator for the Smartfan project. The aim is to produce this complex part with compression molding technique. This results in a reduction of the production costs, allowing the part to be more suitable for the large scale production. The wing will also include a self-sensing system to monitor the damage state.
To achieve this ambitious result, the parts composing the wing (i.e., the outer shells and the bulkhead), were completely redesigned for compression molding. The design of the tooling is currently under development, however, a first layout of the tooling was obtained (in the first figure, the tooling for the production of the structural bulkhead is depicted).
A mold with movable parts to produce the outer shell with the presence of an undercut is under development and will be completed in the next weeks (second figure).
In addition, a tooling for the bonding of the structural components will be developed in the next weeks.
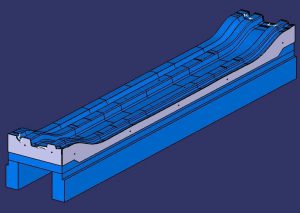
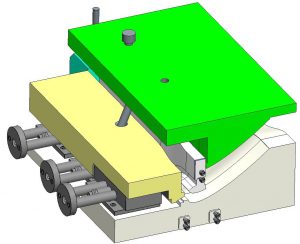
Carbon Fibre Activities (CANOE)
Within the scope of SMARTFAN, CANOE is actively developing formulations and processes for nano-enabled sizing systems for carbon fibres. Main objectives are the improvement of both mechanical properties (Inter Laminar shear strength) but also but electrical conductivity of carbon fibre reinforced polymers (CFRP).
Using different kinds of nano-fillers commercially available or synthetized by NTUA, fibres are sized by CANOE and processed into CFRPs by infusion (CANOE) or pre-preg manufacturing and lay-up (INEGI). These developments have led to promising results for applications in high-end structural applications for instance.
On the other hand, CANOE is particularly involved in the manufacturing of fibres, especially from bio-based materials such as cellulose or lignin as well as carbon fibres therefrom. To complete the existing carbonization line in CANOE – on which SMARTFAN sizing developments at larger scale will be performed – a wet-spinning pilot line will be installed during summer 2020 in CANOE facilities in Lacq. This solvent spinning line will be able to produce around 3 tons of fibers per year, and will allow the spinning of various types of polymers, such as cellulose, polyvinyl alcohol, lignin, polyacrylonitrile, alginate, after dissolution in a solvent like phosphoric acid, water, DMSO, ionic liquids, among others.
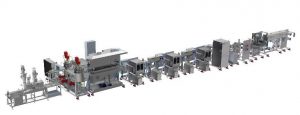
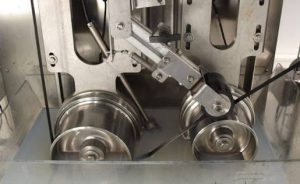
Axial fan design and laboratory tests (ELICA)
In accordance with SMARTFAN goals, ELICA carried out a CFD (Computational Fluid Dynamic) optimization process in order to define the geometric properties of an axial fan (blades number and their shape in particular) to obtain maximum values of the Fluid Dynamic Efficiency (FDE), according to geometric constraints of the technological application.
On the other hand, standard safety tests were performed on plates and on a 3D printed axial fan (designed after the CFD results, shown in fig.2), moulded with different materials.
Safety tests showed that the use of the CNT filled polymer is not allowed for range hoods, but only for air treatment applications. Given the minor progress with a PP V-0 polymer, it might be interesting to test a PP with a better flammability (5VA) index of the matrix, keeping in mind that usually 5VA polymers are unsuitable for impeller moulding.
During next phase, both electrical resistance tests and fluid dynamic performance tests will be carried out on the axial fan. In particular, the impeller will be installed in a standard application to verify materials and life test.
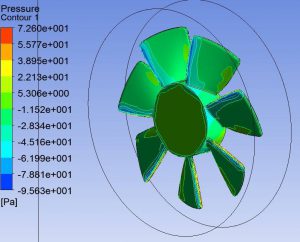
Figure 1
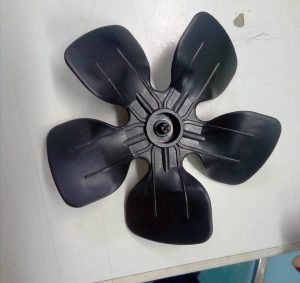
Figure 2
Research Highlights: 3D printing of Smart-Fans (NTUA) (ELICA)
3D printing technology has been exploited within SMARTFAN project in order to manufacture Smart-Fans for ELICA S.P.A. NTUA used an Industrial Markforged X7 3D printer, part of the SMARTFAN’s Pilot Line. This printer utilizes dual printer heads to print both composite, non-composite materials, reinforced or not with carbon fibres using a variety of filaments. Using the dual heads, the printer can produce complex lightweight items, while laser inspection scans parts mid-print to ensure dimensional accuracy for the most critical tolerances. Eiger Slicer, which is compatible with Markforged X7 3D printer, was used for the creation of .mfp file.
A polyamide-based thermoplastic filament has been used, reinforced with chopped carbon fibres and flame – retardant additives, in order to fulfil the requirements of ELICA S.P.A., regarding the flame-retardant properties of the fans that are intended to be used in domestic applications.
NTUA used designs by ELICA for the Smart-Fans and printed 5 prototypes. Also, 20 SDT plates were printed for ELICA to carry out various flammability measurements:
GWIT: Glow-wire Ignition Temperature
GWFI: Glow Wire Flammability Index
NFT: Needle-Flame Test
BPT: Ball Pressure Test
Development of bioinspired 3D printed processor cooling system and establishment of continuous CFs 3D printing pilot line (BIOG3D)
Within SMARTFAN, BioG3D is responsible for the design and development of a 3D printed processor cooling system with smart functionalities such as improved heat flow and self-morphing properties, by employing the composite filaments fabricated within the project. Up to M24, the design of the heat sink has been set, the thermoplastic materials (both composite and neat) that will be used in each part of the heat sink have been finalized and 3D printing process parameters have been optimised for each different material. Pre-programmed architectures with autonomous self-morphing properties and controlled bending function have been implemented by introducing auxetic patterns. In the upcoming period the heat sink design will be further elaborated, and design specifications will be optimised to achieve increased functionality in terms of heat flow and optimal air flow through responsiveness to thermal stimuli.
BioG3D has also established a pilot line for manufacturing 3D printed bioinspired structures, incorporating an FFF 3D printing system, 3D scanner and 3D design software for 3D model development and an infrared thermal camera for monitoring thermal managing materials. To facilitate the use of this pilot line, targeted protocols and recommendations regarding process parameters modifications and materials behavior have been created. Additionally, towards the development of a 3D printing system that can accommodate continuous CFs 3D printing, a modified heatblock of a commercial FFF 3D printer is under development to print both thermoplastic materials and continuous CFs simultaneously. The innovative heatblock, will be used in SMARTFAN’s pilot line, allowing the use of different abrasive materials in combination with thermoplastic filaments.
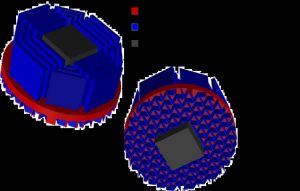
Figure 1. Heat Sink 3D model
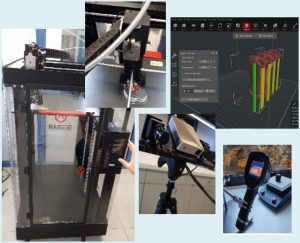
Figure 2. Pilot line equipment
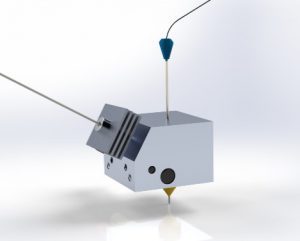
Figure 3. Modified 3D printing heatblock
Evaluation and characterisation of Microcapsules (UOB)
The mechanical properties of self-sensing microcapsules fabricated by ITA have been evaluated by a micromanipulation technique and the ruptured capsules have been analysed at UOB in the last 6 months. Single microcapsule with a diameter up to f200 µm is placed between two parallel surfaces made of a force transducer probe and sample stage of a microscope to a given deformation or rupture at a pre-set speed, and the force imposed on the microcapsules can be measured simultaneously. The diameter of each particle is determined from its image under the microscope. Multiple capsules are randomly selected for the compression test and the statics result are used to analyse the relationship of rupture force, displacement and stress with the size of the capsules. The capsules are freezing cut and dried with ethanol, and thus the ruptured capsules can be observed and characterised under SEM/TEM. This will help to correlate the mechanical strength of the capsules and their microstructure for the improvement of the design and fabrication of the microcapsules.
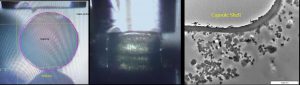
Self-healing capsules (FORTH)
· One of the main tasks of Forth during this period was the production, characterization and provision to SMARTFAN partners of Self-healing capsules.
· Initially the optimal sequestration method for the healing agent and polymerizing agent has to be determined. This sequestration can be achieved through encapsulation or phase separation.
· The standard recipe for the preparation of PUF/DCPD microcapsules was adapted from that of Brown et al. [1].
· In order to confirm that DCPD monomer was enclosed in the UF capsules DSC measurements were taken place.
· To evaluate the healing effect of self-activated samples fracture toughness test was also held, similarly to GFRP system up to 50mm displacement. The modified CFRP samples presented the same mechanical behaviour as the neat (virgin) samples. For the modified specimens, at the end of the first loading, they restored to their initial status (zero loading) and left to heal for 48 hours. The results were promising as the modified specimens reached an average 80% of their initial maximum load.
The abovementioned research was carried out during the M12-M24 period of the project, mainly as a part of Work Packages 1 & 2.
[1]Brown, E.N., Kessler, M.R., Sottos, N.R. & White, S.R. 2003. In situ poly(urea-formaldehyde) microencapsulation of dicyclopentadiene. Journal of Microencapsulation 20: 719-730.
Fabrication of large surface electrodes for supercapacitors using spray-gun deposition method (THALES)
During the last six months, we were able in collaboration with FORTH to spray mixture of Graphene nanoplatelets (GNP) and Carbon Nanotubes (CNTs) on a large surface of 30cmx30cm.
The spray has been performed on commercial aluminum collectors that are usually used for supercapacitors. In this way we have implemented a process that can be easily up-scaled for industrial production of low-cost supercapacitors electrodes.
In the next months we will perform tests using different mixtures of GNP and CNTs at different concentrations in order to define the best compromise in term of capacitance and power delivered.
This is the first time that a deposition by spray on a so large surface is performed. This is the state-of-the-art of the technique.
Before the end of the project this technique will be implemented on the new roll-to-roll machine that will be delivered. Thanks to that we can predict an industrial production in the next two years.
We will implement also this technique in the frame of SMARTFAN for spraying on fabrics in collaboration with NTUA and FORTH for automotive applications. This work is in progress.
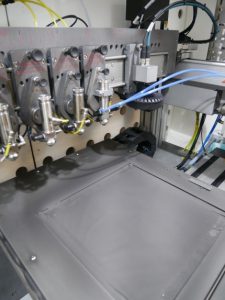
Electrodes obtained through spray-gun deposition method of GNTS/CNTs
Shape memory polymer composites for grabbing devices (UNITV)
The Department of Industrial Engineering of the University of Rome Tor Vergata has produced the first lab-scale prototype of a smart grabbing device with shape memory polymer composites (SMPC) and integrated heating system. This device is obtained by assembling SMPC “fingers” to form the grabbing hand. Compression molding was used to manufacture carbon fiber laminates with interposed shape memory layer. The proposed architecture of the finger allows producing functional modular structures with different operational configurations. External power supply devices were used to provide the required voltage (22 V) to heat the device for both memory and recovery phase of the grabbing devices. Different tests were performed on flat objects (PCB) to show the grabbing ability and good results were achieved. Next steps will be to scale up the size of the grabbing device and to automate the memory stage of composite assembly. The use of consolidated manufacturing technologies and the interesting properties of the SMPCs are the driving forces for their diffusion for “in Space” and “on Earth” applications.
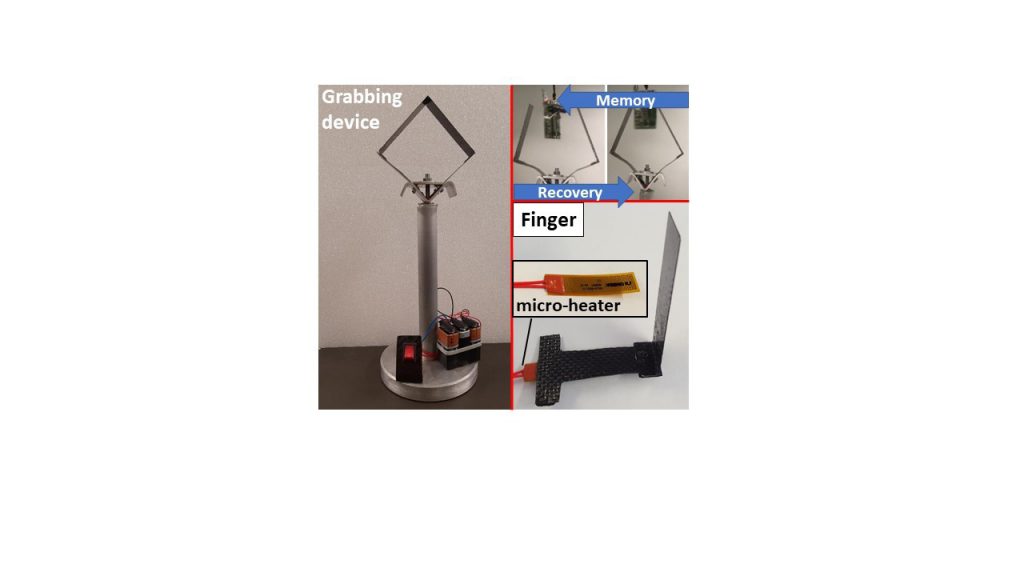