Main Technical Achievements M36
Techedge activity on SMARTFAN
Last month’s Techedge efforts were focused on developing AI models ready to be deployed on ultra-low power IoT devices (as the Arduino BLE 33 Sense), working on real-time data acquired using several types of sensors (audio, roto-vibrational, video). A key aspect here is the fine tuning of the features extracted from data, since a proper features engineering allows to:
- Decrease the amount of dirty data to be ingested by the AI, thus decreasing the computational cost of the AI itself
- Increase the AI accuracy
- Gives news insights on the problem which is under investigations.
Our principal feature engineering approach is based on spectral analysis techniques.
We tested ultra-low power AI application for anomaly detection of tests components using vibrational a sound data. This testing step was necessary in order to optimize neural network models in the perspective to be used with the data coming from SmartFan partners. Following this step, we plan to perform several tests on different architectural solutions, using different neural network configurations as:
- RBM
- Autoencoders
- Convolutional 1D NN
Contact [email protected] for further details.
Self-healing capsules (FORTH)
· One of the main tasks of Forth during this period was the production, characterization and provision to SMARTFAN partners of Self-healing capsules.
· Initially the optimal sequestration method for the healing agent and polymerizing agent has to be determined. This sequestration can be achieved through encapsulation or phase separation.
· The standard recipe for the preparation of PUF/DCPD microcapsules was adapted from that of Brown et al. [1].
· In order to confirm that DCPD monomer was enclosed in the UF capsules DSC measurements were taken place.
· To evaluate the healing effect of self-activated samples fracture toughness test was also held, similarly to GFRP system up to 50mm displacement. The modified CFRP samples presented the same mechanical behaviour as the neat (virgin) samples. For the modified specimens, at the end of the first loading, they restored to their initial status (zero loading) and left to heal for 48 hours. The results were promising as the modified specimens reached an average 80% of their initial maximum load.
The abovementioned research was carried out during the M12-M24 period of the project, mainly as a part of Work Packages 1 & 2.
[1]Brown, E.N., Kessler, M.R., Sottos, N.R. & White, S.R. 2003. In situ poly(urea-formaldehyde) microencapsulation of dicyclopentadiene. Journal of Microencapsulation 20: 719-730.
Multifunctional nanocomposites and carbon fiber reinforced polymers (CFRPs) with enhanced performance (INEGI)
In the past few months, INEGI developed multifunctional and multiscale CFRPs with improved mechanical performance aiming to be used on the demonstrator production: an energy absorber for the automotive industry (manufactured by Dallara).
According to the mechanical characterization performed, the introduction of different loadings of block copolymers (BCPs) in the epoxy matrix resulted in nanocomposites having enhanced tensile and impact strength up to 64 and 25 %, respectively. Based on the scanning electron microscopy (SEM) images below, it is possible to observe the formation of nanostructured BCP spheres that are homogeneously dispersed in the matrix and the roughness of the fractured surface of the tensile specimens, evidencing the presence of toughening paths.
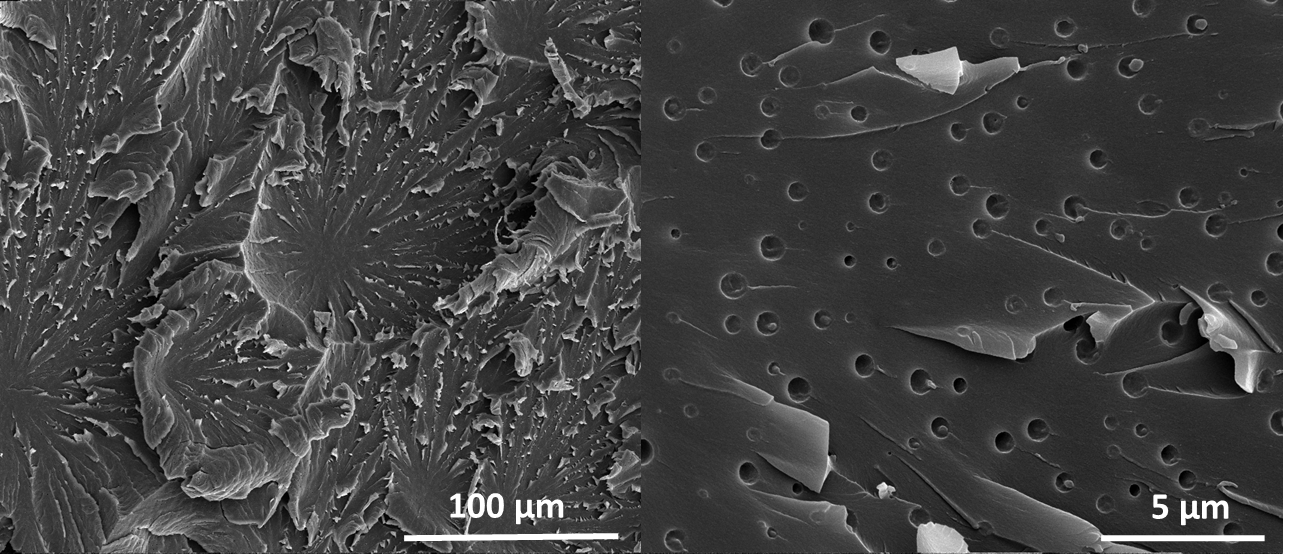
Multiscale pre-impregnated materials and CFRPs were also prepared using modified matrices with BCPs for double cantilever beam (DCB) tests. In Figure 2, it is visible a scheme of the production of prepreg materials, CFRP consolidation in an autoclave and a DCB test. The modified CFRP composites with 2.5 and 5.0 wt. % BCP exhibited impressive improvements on the interlaminar fractured toughness between 55 and 83 %, respectively.
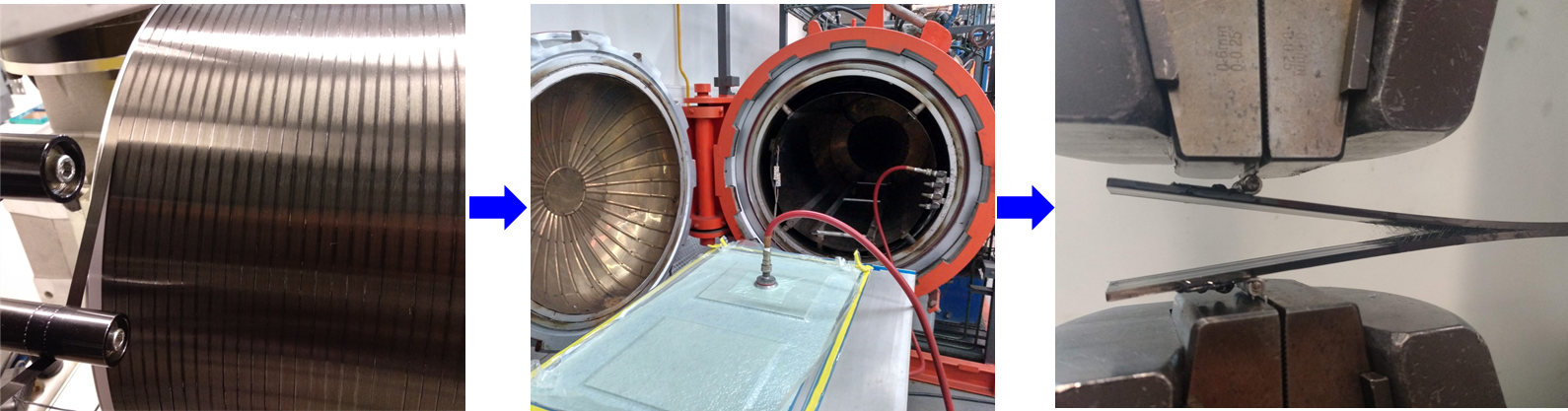
Development of a prototype 3D printer extruder to support continuous fiber 3D printing (BIOG3D)
- Towards the development and validation of new sets of performant thermoplastic composites, BioG3D is developing an open-materials prototype 3D printer extruder for composite production with tailored fiber placement, enabled by Coaxial Continuous Fiber 3D Printing.
- During the last 6 months, redesign and modification of an FFF printhead was conducted.
- Design alterations and prototyping of the modified print-head integration bracket, X-axis carriage grip, fan holder and heatblock were conducted in order to support in-nozzle impregnation of twisted Carbon Fiber (CF) multifilaments with thermoplastic materials in filament form.
- Testing of the prototype 3D printing feeding system is in progress, by employing custom G-code scripts in order to fine-tune material feed rate, printing temperature and printing speed.
- Advanced toolpath generation algorithms are also in development to demonstrate a digitalized manufacturing workflow of 3D printed composites with complex bioinspired structures and advanced materials.
- During the next phase, the printability assessment of thermoplastic matrix and interaction with continuous fiber reinforcement will be conducted to assess properties and performance of the output 3D printed composite material/structures and provide feedback for process optimization and fabrication strategies to be pursued.
- This approach allows to produce free-form, CF composites with continuous fiber reinforcement, without the need for expensive facilities and equipment, such as autoclaves and complex rigid molds, while combining low-cost equipment and advanced feedstock materials for an application-driven production of high-performance components.
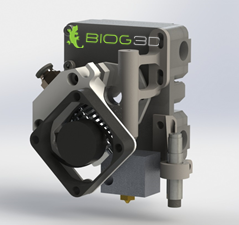
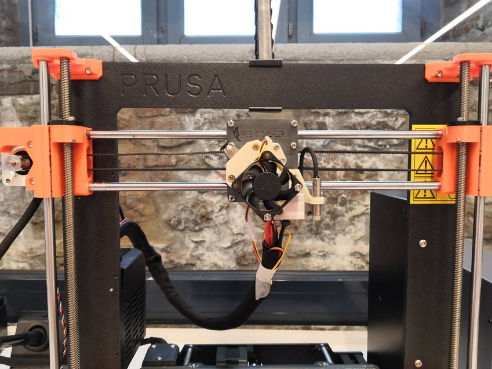
NUMERICAL MODELLING OF SHAPE MEMORY POLYMER COMPOSITE STRUCTURES (UNITV)
The Department of Industrial Engineering of the University of Rome Tor Vergata has started its numerical modelling activity to simulate the shape memory behavior of smart composites. The case study is the prototyped smart finger prototype which has been investigated to validate numerically experimental findings. In the developed FEM model a shape memory polymer (SMP) interlayer was placed between carbon fiber reinforced (CFR) skins.
The first part of the simulation aimed at evaluating the stiffness of the shape memory polymer composite (SMPC) finger by varying the number of the CFR skins. The second part aimed at evaluating if the triggering effect of the polymer transition for shape memory behavior could be modelled by means of changes in the material damping coefficient.
Positive results will allow implementing a full thermomechanical analysis to replicate the experimental shape memory curves, and having a powerful instrument to predict the behavior of large grabbing devices during operation. In fact, next steps will be simulating large grabbing devices to find the best strategy for the memory and recovery phases. Numerical analysis and manufacturing technology are a winning combination for the development of efficient and reliable SMPC devices for “in Space” and “on Earth” applications.
Contact person:
Prof. Fabrizio Quadrini ([email protected])
Prof. Loredana Santo ([email protected])
Ing. Leandro Iorio ([email protected])
Ing. Marco Regi ([email protected])
Ing. Leandro Iorio ([email protected])
Department of Industrial Engineering, University of Rome Tor Vergata
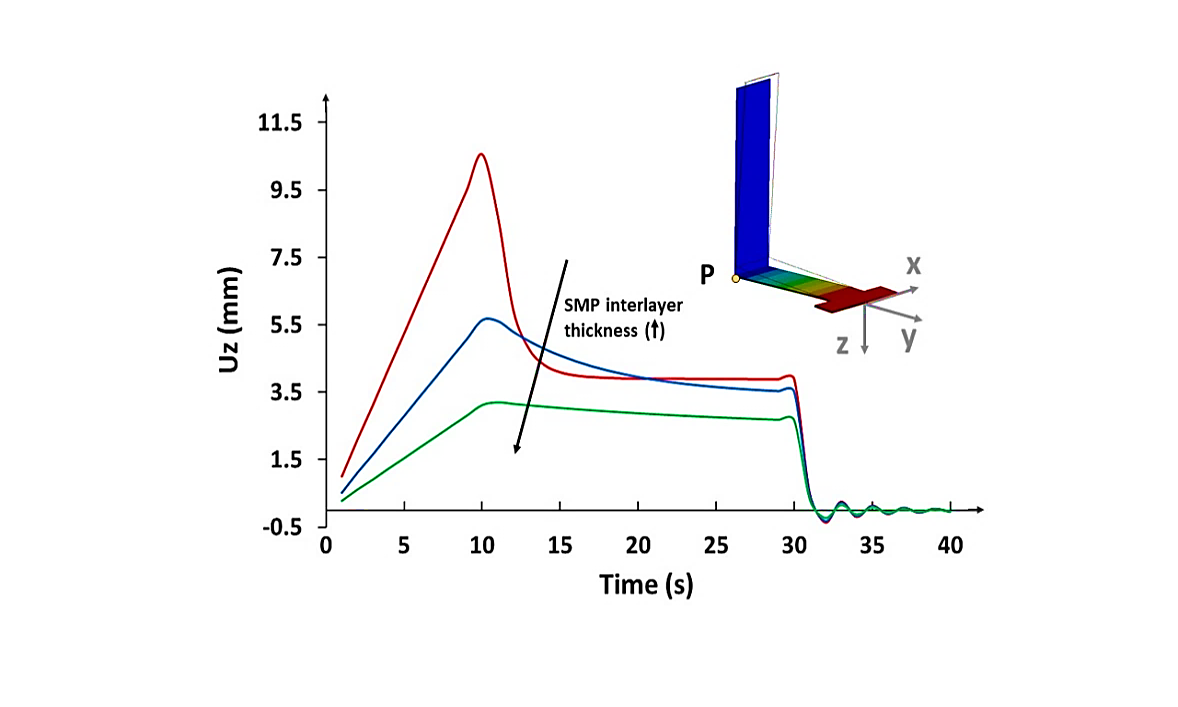
CNT/CNF High energy aerosol generation nanomaterial Dispersion/Suspension processes SMARTFAN
Decision tree & Safety recommendation report (IRES)
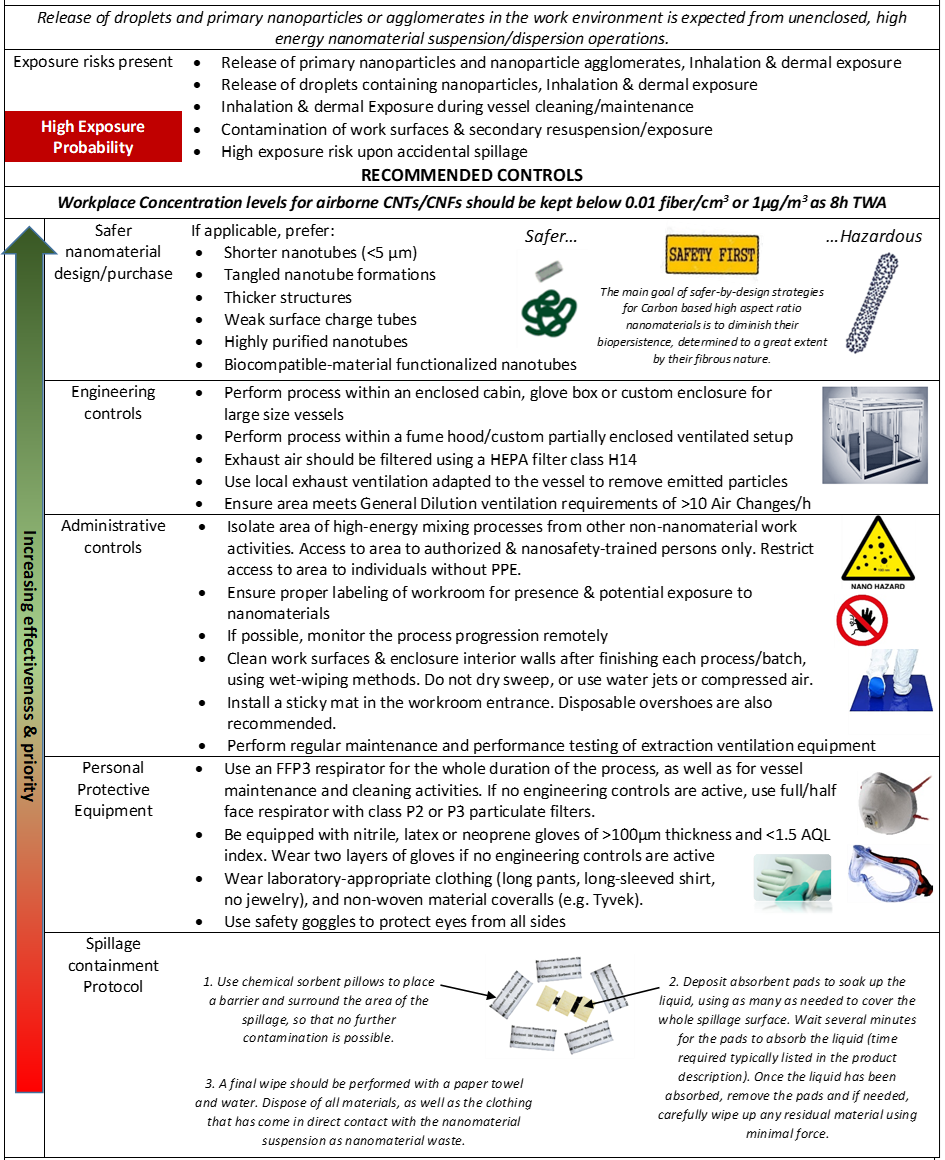
Contact Person: Elias Koumoulos
Email: [email protected]
STRATOSPHERE new activities for SMARTFAN
Stratosphere SA, is in the final phase to test and validate its 16 electrodes Electric Impedance Tomography (EIT) equipment. Some tests are being carry out with carbon fiber reinforced polymers (CFRP) with graphene oxide mixed on the matrix developed in the project, and commercial available CFRP’s.
The objective is to have an integrated platform with hardware to acquire and generate the electric signals, software to control all the steps, simulation and optimization in the same packet. It is possible to read a 2D geometry from a CAD file and make all the analysis with simulation and compare the results with a real structure with electrodes bonded on it and the signal’s generated and read by the hardware developed to validate all the concept. Some useful tools are incorporated, like a virtual electrode position software to select the best points to put the electrodes using a simulated environment. A signal integrity tool was developed to verify the quality of the measurements took during the readings with the hardware.
The software tool gives an image with the absolute or relative conductivity of the measured sample, with different algorithms to detect damage on its interior.
This development was start at the beginning of the Smartfan project, with several improvements during the duration of the task, starting with 8 electrodes version to have 16 electrodes actually with several solvers to predict the electric conductivity.
Actually the EIT equipment is in a final phase with some cases to validate the algorithms and the electronic hardware to achieve TRL6.
This work was carried out by the stratosphere engineers: Nelson Ferreira and Christophe Fernandes.
This task is included in the work done in Task 3.3.1: Thermoset-based smart CFRP.
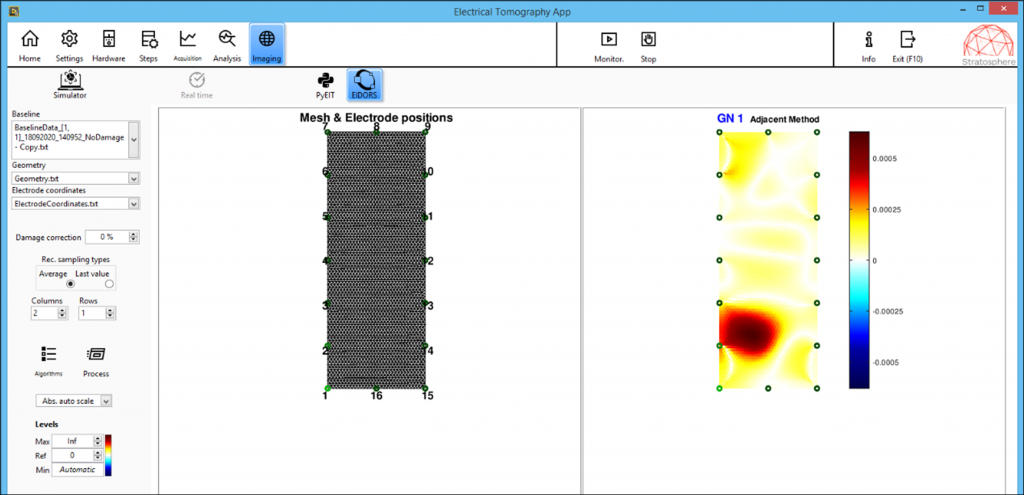
ELICA ACTIVITIES ON SMARTFAN
Last month’s Techedge efforts were focused on two main topics: final design of the new impeller to be used in the new hood that is under development and final test to identify the proper raw material to be used to manufacture the new impeller
The new impeller is not so different from former simulation results. Just few adjustments have been made to fit the impeller in both application ELC wants to develop
Several raw materials have been supplied to CANOE for proper functionalization and then tested according to self-extinguish requirements. Finally, it seems that a material has been identified. As per following table 5VA PPHO + 20 % talc compounded with 5% CNT by CANOE fulfil all requirements.
Contact Francesca Ravanelli ([email protected]) or Alessandro Florio ([email protected]) for further details.
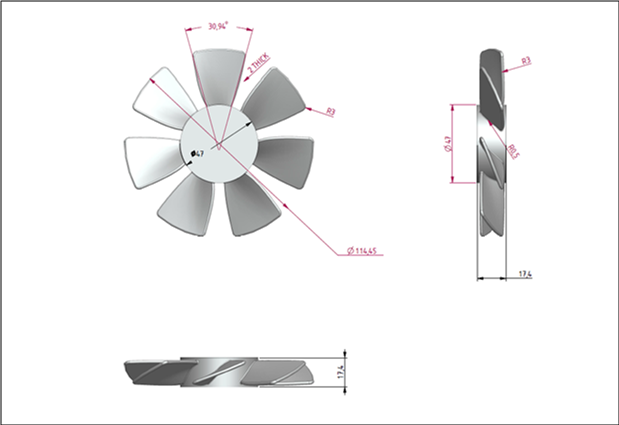
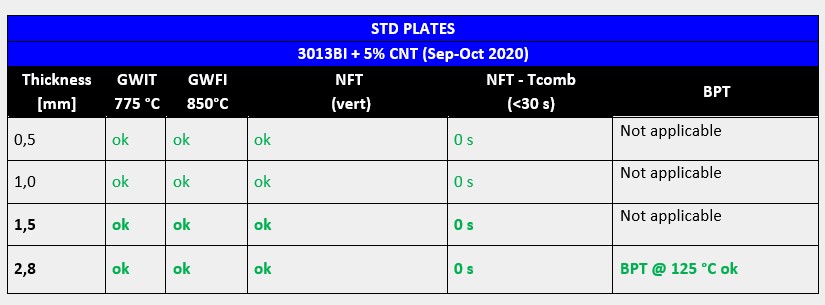
SMART DEMOS FOR AUTOMOTIVE INDUSTRY (DALLARA)
In the frame of the Smartfan project, Dallara Automobili is developing an innovative front wing for the racing car sector.
The part was redesigned in an innovative way if compared with the traditional wings, with the aim of achieving the maximum product quality, in combination with a reduction of the production costs.
Prepreg carbon patches are initially preformed through a semi-automated process that involves the use of a vacuum bench. The preformed plies are subsequently placed into a mold and the final shape is obtained by compression molding. A specific tooling was designed to produce a part with an undercut geometry.
This process presents a number of innovations, including highly repeatable quality of the part, high strength and stiffness combined with lightweight.
In addition, the labor intensity required for the production of the part was significantly reduced. The time for the manufacturing of the part was reduced of more than 50%, with a resulting beneficial effect on the production costs of the part.
For further information do not hesitate to contact us at [email protected]
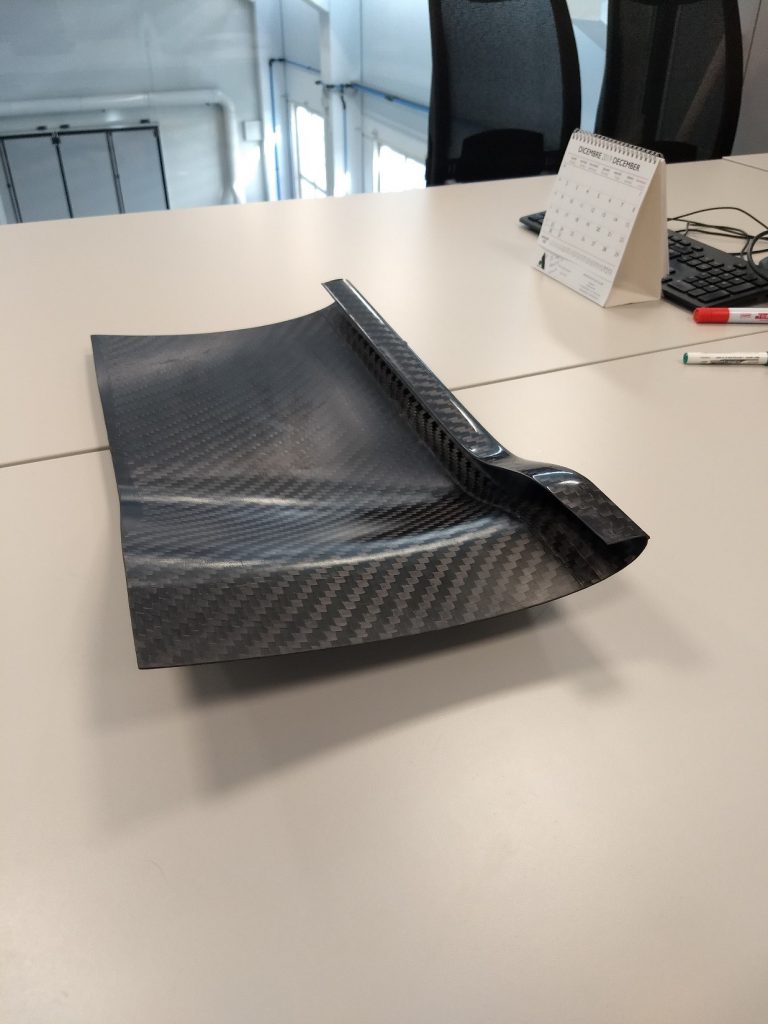
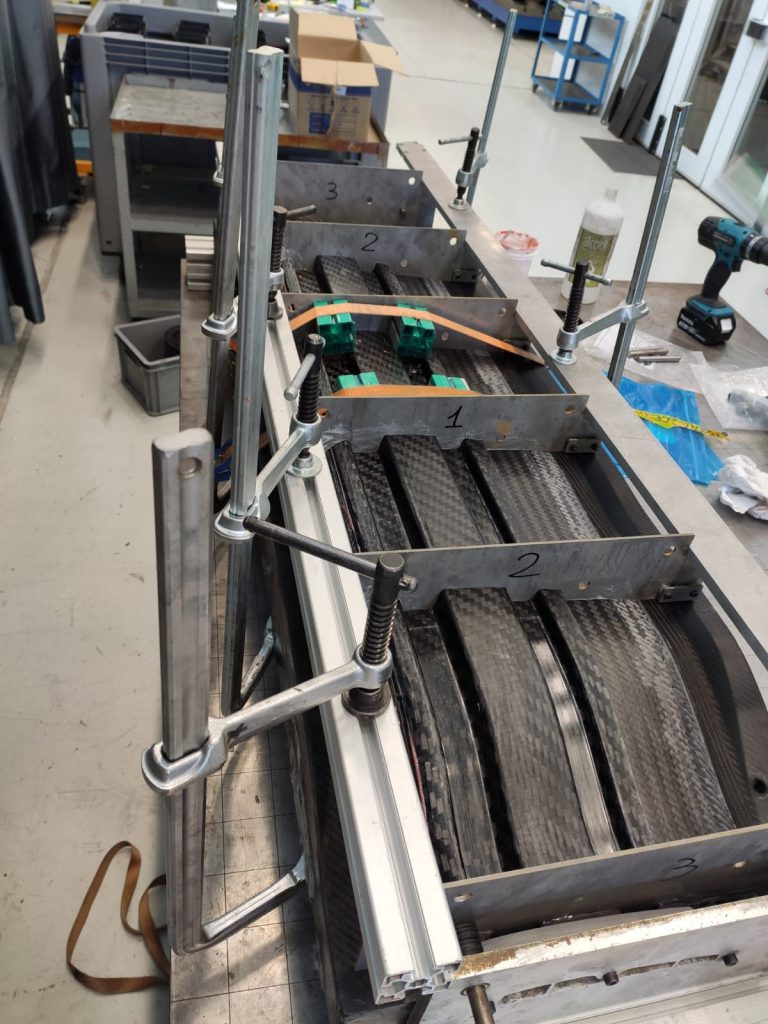